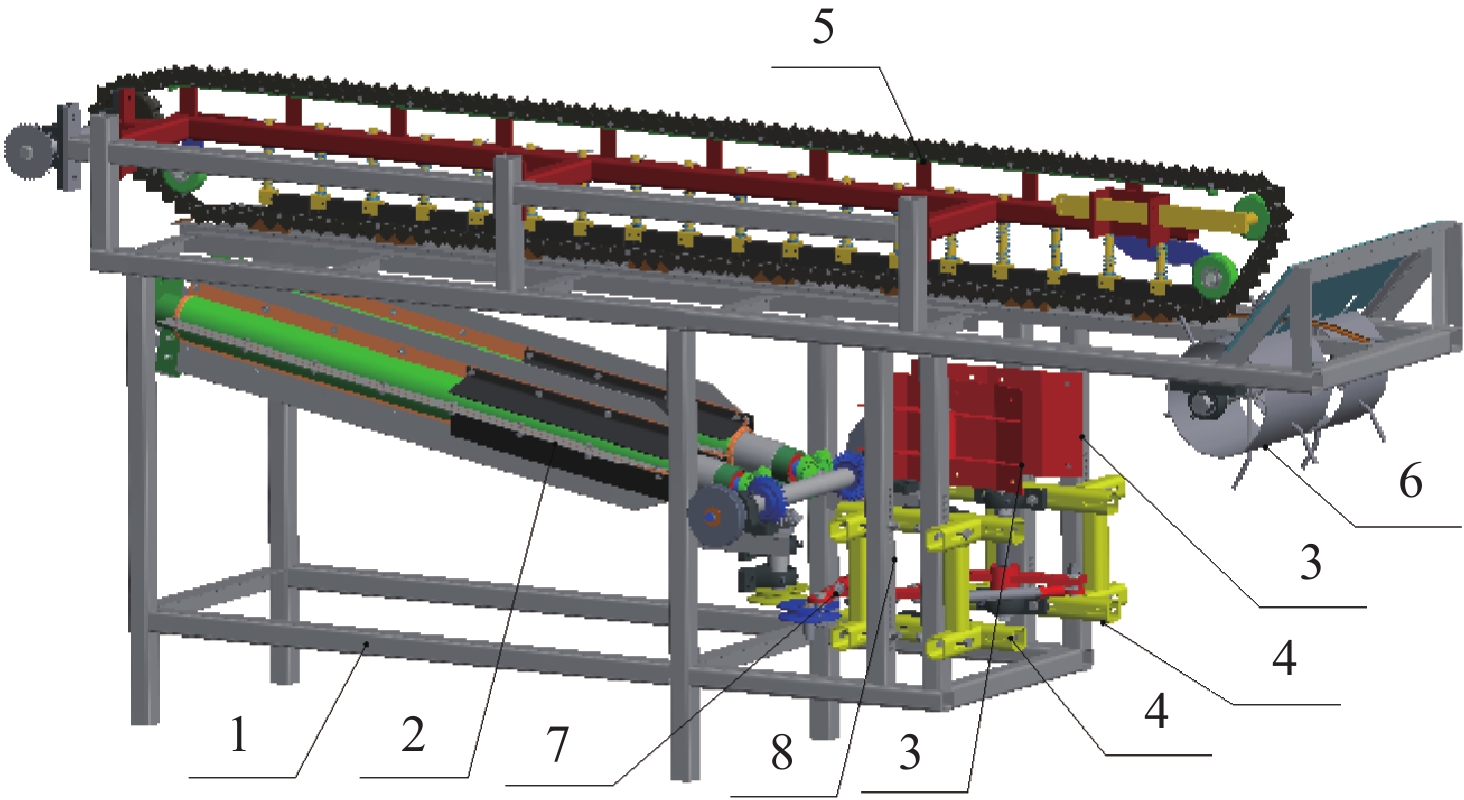
Citation: | Wang S Y, You Z Y, Sun D W, Xiao Q, Luo Q J, He L. Performance test of a half-feed peanut-cleaning picker suitable for clay hill areas in southern China. Int J Agric & Biol Eng, 2024; 17(4): 1–9. DOI: 10.25165/j.ijabe.20241704.8782 |
To solve the problems of excessive soil lumps, broken branches and seedlings in pods and difficulty in removing impurities in the harvested pods of peanuts in the hilly areas of southern China, which is due to the high soil viscosity and easy hardening, and to improve the soil removal effect of the peanut half-feed pod picker in hilly areas of China, this article designed a half-feed peanut-cleaning picker suitable for southern clay hilly areas and provided a detailed introduction to the overall structure, working principle, and adjustment methods of various operating parameters. Through field measurement experiments, the influencing factors and laws of soil removal performance indicators, such as the comprehensive soil removal rate and POD drop rate, were studied. The results showed that the comprehensive soil removal rate gradually increased with increasing soil patting frequency, soil patting amplitude, and picking roller speed, first increased and then decreased with increasing picking roller gap and gradually decreased with increasing soil patting plate gap and clamping conveyor chain speed. The comprehensive soil removal rate of the soil patting plate using the opposite patting method was greater than that of the swinging patting method. The soil removal pod drop rate increased gradually with increasing soil patting frequency and amplitude and decreased with increasing soil patting plate gap and clamping conveyor chain speed. The soil removal pod drop rate of the soil patting plate using swing patting was lower than that using the opposite patting method. The speed and gap of the picking roller had no effect on the soil removal pod drop rate. The frequency, amplitude, form, and gap of the soil patting plate had extremely significant impacts on the rate of decrease in the number of soil removal pod drop rate. The clamping conveyor chain speed had a significant impact, while the speed and gap of the picking roller had no significant impact. The influence of all factors on the comprehensive soil removal rate was extremely significant. This study provides a theoretical basis and technical reference for parameter optimization research on peanut-cleaning picking machines in the clay hilly areas of southern China.
Peanut has become one of the fastest growing oil crops and cash crops in the world, second only to soybean in world oil production and trade, playing an important role in the safety of the world’s edible oils[1-3]. According to the statistics of the World Food and Agriculture Organization (FAO), in 2022, the peanut planting area in China was 4.46×106 hm2, with a yield of 1.84×107 t, both of which are among the highest in the world. However, the mechanization level of peanut harvesting in China is relatively lagging behind that in the United States, Brazil, Argentina, etc. Most peanut planting areas are still dominated by manual and semimechanized harvesting[4-8], especially in the clayey soil areas of the south, where manual harvesting is still the main method[9]. In 2021, the mechanized harvest level of peanuts in China was only 50.9%[10], and it was even lower in southern hilly clayey soil areas, which seriously restricted the development of the peanut industry.
In the southern clayey soil area, local farmers usually pull up peanuts by hand after the soil loosens after rain and then use small peanut-picking machines for pod picking operations. However, due to the high soil viscosity and easy compaction, many soil lumps remain on the pulled peanut seedlings, and due to the lack of special peanut-picking and harvesting machines suitable for the southern clayey soil area, the harvested peanut pods contain soil lumps, broken branches and seedlings, which are difficult to clean and require manual sorting, which seriously restricts the development of the peanut industry in this region.
At present, there is no special half-feed soil removal device in the southern clay hilly area on the market. When peanuts are fully fed and harvested in the main production areas of the north, the soil removal work is mostly completed during the process of picking, conveying, picking and sorting. When half-feeding for combined harvesting, a small amount of sand or sandy loam soil is often removed from the peanut seedlings by shaking the soil plate. These devices are not suitable for peanut harvesting in the southern region, which has sticky soil. Therefore, conducting research on the methods and technologies for clean peanut-harvesting in southern clayey soil has important practical significance for improving the mechanization level of peanut harvesting, reducing labor intensity, improving the cleanliness of peanut pods, and facilitating the agricultural season in the hilly areas of southern China.
Research on peanut harvesting technology abroad can be divided into two main methods: full feeding and half feeding. Full feeding is mainly practiced in the United States, while half feeding is practiced in South Asian and Southeast Asian countries such as India and African countries such as Nigeria[3,11]. Full-feed harvesting, practiced in the United States, involves early research, high mechanization, and high efficiency, making it suitable for large-scale peanut harvesting. Countries with similar peanut production conditions, such as Brazil, Australia, and Argentina, also mainly use full-feed harvesting[12,13]. However, due to the sandy loam soil in which peanuts grow, the United States often uses perforated screens to remove a small amount of fine soil, and there are few reports on clean removal techniques for clayey soil blocks. The mechanization level of peanut harvesting in South Asia, Southeast Asia and African countries such as India is even lower than in China, which mainly relies on manual labor, so clean picking technology has not been studied.
At present, research on peanut harvesting technology in southern sticky soil in China has focused mostly on peanut digging and plucking machines and small harvesters[14-19], while academic research on clean harvesting technology for half-feed peanut-cleaning pickers in sticky soil is rare. Relevant research on clean crop-harvesting technology has focused mostly on potato and sweet potato harvesters[20-22].
In view of the above problems, this study aims to carry out performance tests on the basis of a predesigned half-feed peanut-cleaning picker suitable for the southern clay hilly area to provide a theoretical basis and technical reference for parameter optimization research on peanut pickers in the region. The main research objectives are as follows: (1) design a half-feed peanut-cleaning picker suitable for southern clay hilly areas; (2) analyze the adjustment methods of key operating parameters; and (3) conduct field performance experiments on the effects of various operation parameters on soil removal efficiency.
Based on research on peanut varieties, planting patterns and soil characteristics in southern China, a half-feed peanut-cleaning picker suitable for the clay hilly area of southern China was designed. As shown in Figure 1, the machine is mainly composed of a picking device, soil removal device (mainly composed of a soil tapping plate, soil tapping plate installation adjustment frame, soil tapping device driving mechanism), clamping and conveying device, seedling feeding mechanism, and transmission system. It mainly completes operations such as peanut seedling feeding, clamping and conveying, patting and removing soil, and peanut pod picking. The main parameters are listed in Table 1.
Items | Value |
Picker size (length × width × height)/mm | 2600×950×1080 |
Distance adjustment range between soil removal device and clamping conveyor device/mm | 30-100 |
Distance adjustment range between soil removal device and picking device/mm | 50-200 |
Total mass of the picker/kg | 250 |
Matched power/kW | 3.3 |
Power-source form | Single cylinder gasoline engine |
Rated speed of power source/r·min–1 | 1800 |
When working, the peanut seedlings move backward along the lower conveying guide rail under the push of the tooth of the feeding mechanism and the interaction with the clamping chain of the clamping conveying device. When passing through the soil removal device, the soil on the peanut seedlings is patted and dropped under its flapping action, and the remaining clean seedlings enter the picking device under the drive of the clamping conveying device. The pod is picked under the action of the roller. At the same time, the upper and lower positions, front and rear positions, and the patting amplitude and frequency of the soil removal device can be adjusted through the soil patting plate installation adjustment frame and driving mechanism.
The peanuts of the Nanjing Luhe Peanut Experimental Base were selected as the test material, and the selected field soil was clay. The variety is Su Nonghua No. 1, which has a single ridge and a double row. The average ridge spacing is 750 mm, and the average plant spacing is 250 mm. The average peanut plant height is 480 mm, and the pod height ranges from 0-110 mm.
The main equipment and instruments used were a 5HZ-175 peanut excavator harvester, Kaifeng 796 electronic scale (measuring range 30 kg, resolution 1 g), Zhejiang Topu TZS-I soil moisture measuring instrument (measurement range 0-100%, resolution 0.1%, relative percentage error ≤3%), tape (measuring range 5 m, accuracy 1 mm), Fluke 931 tachometer (measuring range 1-
According to NY/T 502-2016 “Quality of Peanut Harvester Operations”[28] and NY/T 2204-2012 “Technical Specification for Quality Evaluation of Peanut Harvesters”[29], five sample areas were randomly selected from the experimental field for testing, each with an area of 4 m×4 m. Before the experiment, the peanut seedlings were excavated using the commonly used 5HZ-175 peanut excavator harvester on the market and then placed in the field for natural drying for 1 to 2 d. The moisture content of the peanut seedlings ranged from 25% to 45%, and the moisture content of the mud blocks ranged from 15% to 20%. The hardness of the mud blocks ranged from 50 to 80 Pa. The test conditions are shown in Figure 2.
From the previous analysis, it can be seen that the performance indicators used to measure the soil removal effect mainly include the comprehensive soil removal rate and soil removal pod drop rate, and the main factors affecting the two indicators are the soil patting plate frequency, soil patting plate amplitude (i.e., crank length), soil patting plate form (opposite patting, swinging patting), picking roller speed and gap, gap between the two soil patting plates, and clamping conveyor chain speed. The adjustment methods for each factor are as follows:
(1) Adjustment of the soil patting form: The structure of the soil removal device, which is mainly composed of a soil patting plate, a soil patting plate installation shaft, a seat bearing, a connecting rod, a driving pulley, a driving rocker, a swing rod, and a soil patting plate installation adjustment frame, is shown in Figure 3. The two soil patting plates are installed relative to each other on the installation shaft of the two soil plates and are fixed and locked by a set of locking bolts. The swing rods Ⅰ and Ⅱ are fixed to the two mounting shafts through keys. The swing rod Ⅰ is hinged to the driving pulley through the driving rocker. By using connecting rod Ⅱ to connect the two swing rods, the soil patting plate can swing in the same direction. By using connecting rod Ⅰ to connect the two swing rods, the soil patting plate can swing in the opposite direction.
(2) Adjustment of the soil patting plate amplitude (i.e., crank length): As shown in Figure 3, the crank length and the effective length of swinging rod Ⅰ (Lb) can be changed by changing the hinge position of the driving rocker with the driving pulley (which is designed with installation holes of different radii r, i.e., different crank lengths) and swing rod Ⅰ. Then, the soil patting plate amplitude can be changed. For the preliminary design, r=25, 35, and 45 mm, and Lb=160, 170, and 180 mm.
(3) Adjustment of the soil patting plate gap (i.e., crank length): The installation of the soil patting plate is shown in Figure 3 and Figure 1. The two soil patting plates are connected to the soil patting plate installation adjustment frame through the soil patting plate installation shaft and seat bearing. The soil patting plate installation adjustment frame is connected to the adjustment and installation vertical beam of the soil patting plate through a locking bolt group. There is a waist-shaped hole in the square pipe of the soil patting plate installation adjustment frame. By adjusting the soil patting plate mounting adjustment frame on the installation position of the vertical beam of the soil patting plate and adjusting the length of connecting rod Ⅱ (or connecting rod Ⅰ) and the driving rocker, the gap between the two soil patting plates can be changed.
(4) Adjustment of the soil patting plate frequency: The transmission system of the soil patting device is shown in Figure 4, and the soil patting plate frequency is mainly determined by the speed of the driving pulley. The driving pulley is connected to the main drive shaft of the soil patting device through a belt and a driving pulley. The main drive shaft of the soil patting device is connected to the main drive shaft through a bevel gear, and the main drive shaft is connected to the engine through the driving pulley and belt. By replacing the transmission pulleys with different diameters, the speed of the drive pulleys can be changed, and then the frequency of the soil patting plate can be changed.
(5) Adjustment of the speed and clearance of the picking rollers: The transmission system of the picking device is shown in Figure 5 and Figure 1. The picking roller is connected to the main transmission shaft through the bevel gear of the main transmission shaft, and the main transmission shaft is connected to the engine through the driving pulley and belt. By adjusting the size of the engine throttle or replacing the drive sprocket with different diameters, the speed of the main transmission shaft can be adjusted, thereby changing the speed of the picking roller. There is a waist-shaped hole on the installation adjustment plate of the picking roller. By adjusting the left and right positions of the installation adjustment plate and bevel gear I and locking the bevel gear with the adjustment fixing ring, the clearance between the two picking rollers can be adjusted.
(6) Adjustment of the speed of the clamping conveyor chain: The transmission system of the clamping conveyor device is shown in Figure 6 and Figure 1. The clamping conveyor chain is connected to the auxiliary drive shaft through the clamping sprocket, and the auxiliary drive shaft is connected to the engine through the clamping sprocket and chain. The movement speed of the clamping conveyor chain can be adjusted by adjusting the size of the engine throttle or replacing the drive sprocket with different diameters.
1) Comprehensive soil removal rate
Fifty peanut seedlings were selected from the sampling area for each experiment, and the test was conducted after the speed of each component of the picker stabilized and reached the rated speed. Before the experiment, a canvas was manually laid on the ground below the soil removal device, picking device, and seedling throwing area to collect soil from each part, and the sticky soil on the picked peanut pods was manually removed and measured. A total of 5 tests were performed, and the average value was taken. The calculation formula is as follows:
ηzq=M1+M2M1+M2+M3+M4×100% | (1) |
where, ηzq is the soil removal rate, %; M1 is the mass of soil beaten by the soil removal device, g; M2 is the mass of soil beaten by the picking device, g; M3 is the mass of soil in the picked pods, g; and M4 is the mass of soil left on the seedlings after picking, g.
2) Soil removal pod drop rate
Fifty peanut seedlings were selected from the sampling area for each experiment, and the test was conducted after the speed of each component of the picker stabilized and reached the rated speed. The unpicked pod on the seedling after picking was manually picked, and the peanut pod knocked down by the soil removal device was picked up and cleaned. The weight was measured separately. The test was repeated 5 times, and the average value was calculated. The calculation formula is as follows:
ηql=m2m1+m2+m3×100% | (2) |
where, ηql is the soil removal pod drop rate, %. m1 is the mass of the picked peanut pods, g; m2 is the mass of peanut pods shot down by the soil removal device, g; and m3 is the mass of peanut pods that have not been picked from the peanut seedlings, g.
To further analyze the regularity and significance of the influence of various factors on the performance indicators, single-factor and multilevel repeated tests were conducted, and the test factors and level design are listed in Table 2.
Level | Factors | ||||||
A: Soil patting plate frequency/ Hz |
B: Soil patting plate amplitude (crank length)/ mm |
C: Soil patting form |
D: Picking roller speed/ r·min–1 |
E: Picking roller gap/ mm |
F: Soil patting plate gap/mm |
G: Clamping conveyor chain speed/ m·s–1 |
|
1 | 2.0 | 25 | 1 (Same direction swing) | 275 | 20 | 80 | 0.4 |
2 | 4.0 | 35 | –1 (Opposite direction swing) | 375 | 0 | 100 | 0.6 |
3 | 6.0 | 45 | / | 475 | -20 | 120 | 0.8 |
(1) Influence of the soil patting plate frequency on the soil removal effect
To study the influence of soil patting frequency on the two soil removal performance indicators, according to the common levels of factors used in half-feed peanut pickers, a crank length of 35 mm, clamping conveyor chain speed of 0.6 m/s, soil patting form of –1 (i.e., using opposite patting form), picking roller speed of 300 r/min, picking roller gap of 0 mm, and a soil patting plate gap of 100 mm were used. Each factor level was tested three times, and the results are shown in Table 3. The mean of the repeated experiments was taken, and the results are shown in Figure 7.
Soil patting plate frequencyA |
Comprehensive soil removal rate ηzq/% |
Soil removal pods drop rate ηql/% |
2.0 | 92.18 | 2.28 |
2.0 | 93.20 | 2.69 |
2.0 | 91.79 | 2.72 |
4.0 | 96.75 | 4.77 |
4.0 | 96.48 | 3.94 |
4.0 | 97.24 | 4.39 |
6.0 | 97.83 | 4.43 |
6.0 | 97.69 | 4.45 |
6.0 | 98.11 | 4.95 |
Figure 7 shows that, with increasing soil patting plate frequency, the comprehensive soil removal rate and soil removal pod drop rate gradually increase and tend to stabilize.
SPSS 19.0 software was used to conduct a P value test on the soil patting plate frequency at a significance level of α=0.05, and the variance analysis results are shown in Table 4. The results show that the soil patting plate frequency had extremely significant effects on both the comprehensive soil removal rate and the soil removal pod drop rate. When the soil patting plate frequency varies from 2.0 to 6.0 Hz, the number of times the soil patting plate beats peanut seedlings, mud blocks, and pods per unit time increases. Therefore, the comprehensive soil removal rate and soil removal pod drop rate gradually increase, which has an extremely significant influence on these parameters. However, when the soil patting plate frequency increases to a certain value, the soil and pods that are easily beaten down have already been patted off, and the soil and pods that are difficult to beat down (such as the soil carried in the middle of the seedlings, the soil adhered to the pods, and pods with strong stem connection force) are also not easily patted down after multiple patting (the impact force of the soil patting plate is less than the connection force of some soil and pods). Therefore, the comprehensive soil removal rate and soil removal pod drop rate tended to stabilize after increasing to a certain extent.
Source of variance | Sum of squares | df | Mean squares | F value | Sig. | |
ηzq | Model | 50.867a | 2 | 25.434 | 105.350 | 0.000 |
A | 50.867 | 2 | 25.434 | 105.350 | 0.000 | |
Error | 1.449 | 6 | 0.241 | |||
Sum | 52.316 | 8 | ||||
ηql | Model | 7.500b | 2 | 3.750 | 35.171 | 0.000 |
A | 7.500 | 2 | 3.750 | 35.171 | 0.000 | |
Error | 0.640 | 6 | 0.107 | |||
Sum | 10.102 | 8 | ||||
a. 0.972(R2adj=0.963) b. R2=0.921(R2adj=0.895) |
(2) Influence of the soil patting plate amplitude on the soil removal effect
A single-factor test was carried out for the soil patting plate amplitude, with the soil patting plate frequency taking the optimal value of 4.0 Hz, which is relatively good for both the comprehensive soil removal rate and the soil removal pod drop rate in the single-factor test mentioned above. The other parameter values were the same as those in section (1). Each factor level was repeated three times; the mean value was taken, and the results are shown in Figure 8.
Figure 8 shows that, with increasing soil patting plate amplitude, the comprehensive soil removal rate and soil removal pod drop rate gradually increase.
Given the significance level α=0.05, analysis of variance was performed on the test results, as shown in Table 5. The results show that the soil patting plate amplitude has extremely significant effects on both the comprehensive soil removal rate and the soil removal pod drop rate. As the soil patting plate amplitude increases (i.e., the crank length), under the condition that the soil patting frequency remains constant, the distance that the soil patting plate moves at the same time increases, resulting in an increase in the movement speed of the soil patting plate, which in turn increases the impact force on peanut seedlings, mud blocks, and pods. Therefore, the comprehensive soil removal rate and the soil removal pod drop rate gradually increase, and the impact of the soil patting plate amplitude is extremely significant.
Source of variance | Sum of squares | df | Mean squares | F value | Sig. | |
ηzq | Model | 68.953a | 2 | 34.476 | 222.428 | 0.000 |
B | 68.953 | 2 | 34.476 | 222.428 | 0.000 | |
Error | 0.930 | 6 | 0.155 | |||
Sum | 69.883 | 8 | ||||
ηql | Model | 13.375b | 2 | 6.688 | 102.239 | 0.000 |
B | 13.375 | 2 | 6.688 | 102.239 | 0.000 | |
Error | 0.392 | 6 | 0.065 | |||
Sum | 13.768 | 8 | ||||
a. R2=0.987(R2adj=0.982) b. R2=0.971(R2adj=0.962) |
(3) Influence of soil patting form on the soil removal effect
The soil patting plate amplitude was set at 35 mm, and the other parameter values were the same as those in section (2). A single-factor test was conducted on the soil patting form. Each factor level was repeated three times, and the mean value was taken. The results are listed in Table 6.
Soil patting form C | Comprehensive soil removal rate ηzq/% | Mean of comprehensive soil removal rate/% | Soil removal pods drop rate ηql/% | Mean of soil removal pods drop rate/% |
1 | 92.32 | 92.25 | 2.38 | 2.33 |
1 | 91.98 | 2.21 | ||
1 | 92.44 | 2.41 | ||
–1 | 96.75 | 96.82 | 4.77 | 4.37 |
–1 | 96.48 | 3.94 | ||
–1 | 97.24 | 4.39 |
As shown in Table 6, the comprehensive removal rate and soil removal pod drop rate are both greater when the soil patting plates swing in the opposite direction than when they swing in the same direction.
Given the significance level α=0.05, analysis of variance was performed on the test results, as listed in Table 7. The results show that the soil patting form has extremely significant effects on both the comprehensive soil removal rate and the soil removal pod drop rate. Therefore, it can be concluded that, under the same conditions, the impact on peanut plants increases when the soil patting plates swing in the opposite direction compared to when they swing in the same direction. Soil removal and pod dropping are both due to the impact of the soil patting plate. Therefore, the comprehensive soil removal rate and the soil removal pod drop rate are greater when the soil patting plates swing in the opposite direction than when they swing in the same direction, and the impact on the soil removal performance indicators is extremely significant.
Source of variance | Sum of squares | df | Mean squares | F value | Sig. | |
ηzq | Model | 31.419a | 2 | 31.419 | 305.978 | 0.000 |
C | 31.419 | 2 | 31.419 | 305.978 | 0.000 | |
Error | 0.411 | 6 | 0.103 | |||
Sum | 31.830 | 8 | ||||
ηql | Model | 6.202b | 2 | 6.202 | 67.312 | 0.001 |
C | 6.202 | 2 | 6.202 | 67.312 | 0.001 | |
Error | 0.369 | 6 | 0.092 | |||
Sum | 6.570 | 8 | ||||
a. R2=0.987(R2adj=0.984) b. R2=0.944(R2adj=0.930) |
(4) Influence of the picking roller speed on the soil removal effect
In the above analysis, the soil patting form –1 (that is, opposite direction swing), with better performance for both indicators, was used, and the other parameter values were the same as those in section (3). A single factor test was conducted on the picking roller speed. Each factor level was repeated three times, and the mean value was taken. The results are shown in Figure 9.
Figure 9 shows that, with increasing picking roller speed, the comprehensive soil removal rate first gradually increases and then tends to stabilize, with little change in the soil removal pod drop rate.
Analysis of variance at a significance level of α=0.05 was performed on the test results, as listed in Table 8. As shown in Table 8, the effect of the picking roller speed on the soil removal pod drop rate is not significant but is extremely significant for the comprehensive soil removal rate. The analysis showed that the picking rollers were located behind the soil removal device and did not have a striking effect on soil removal or pod removal; therefore, the rollers had no effect on the rate at which the pods were removed from the soil. However, as the rotation speed of the picking roller increases, the linear velocity of the picking roller blades increases relative to that of the peanut seedlings, which increases the impact on the peanut stem and soil. Therefore, the comprehensive soil removal rate gradually increases first. However, after increasing to a certain extent, the amount of soil remaining on the peanut plants decreased, and the soil in the middle of the peanut plants or pods with a high adhesion force was difficult to remove. Therefore, the comprehensive soil removal rate tends to be stable, and the impact on the comprehensive soil removal rate is extremely significant.
Source of variance | Sum of squares | df | Mean squares | F value | Sig. | |
ηzq | Model | 147.344a | 2 | 73.672 | 288.232 | 0.000 |
D | 147.344 | 2 | 73.672 | 288.232 | 0.000 | |
Error | 1.534 | 6 | 0.256 | |||
Sum | 148.878 | 8 | ||||
ηql | Model | 0.311b | 2 | 0.155 | 1.540 | 0.288 |
D | 0.311 | 2 | 0.155 | 1.540 | 0.288 | |
Error | 0.605 | 6 | 0.101 | |||
Sum | 0.915 | 8 | ||||
a. R2=0.990(R2adj=0.986) b. R2=0.339(AR2adj=0.119) |
(5) Influence of the picking roller gap on the soil removal effect
According to section (4), when the picking roller speed is high, the comprehensive soil removal rate is high, and the soil removal effect is good. However, if the speed is too high, the impact of the picking roller blades on the peanut pods will be too strong, which will increase the damage to the peanut pods. Therefore, the speed of the picking roller should be taken as the value with the best comprehensive soil removal rate in the above analysis, which is 375 r/min, and the other parameter values are the same as those in section (4). A single-factor test was conducted on the picking roller gap. Each factor level was repeated three times, and the mean value was taken. The results are shown in Figure 10.
Figure 10 shows that, with a decreasing picking roller gap, the comprehensive soil removal rate first gradually increases and then decreases, and the soil removal pod drop rate tends to stabilize, with little change.
Analysis of variance at a significance level of α=0.05 was performed on the test results, as shown in Table 9. As shown in Table 9, the effect of the picking roller gap on the comprehensive soil removal rate is extremely significant and does not significantly affect the soil removal pod drop rate. Similarly, in section (4), the picking rollers are located behind the soil removal device and will not have a striking effect on the soil removal and pod drop, so there is basically no change in the soil removal pod drop rate. When the picking roller gap decreases from 20 mm to 0 mm to –20 mm, that is, when the two picking rollers move from gap matching to tangent matching to overlapping matching, the impact of the picking rollers on peanut seedlings, soil, pods, etc., gradually increases, and the soil removal effect gradually increases. However, at the same time, too many broken peanut seedlings will fall off and hang on the long hole inclined plate below the picking device, blocking the leakage of long holes into the soil and causing some of the fallen soil to mix into the collected pods. Therefore, the comprehensive soil removal rate first increased and then decreased.
Source of variance | Sum of squares | df | Mean squares | F value | Sig. | |
ηzq | Model | 26.296a | 2 | 13.148 | 110.654 | 0.000 |
E | 26.296 | 2 | 13.148 | 110.654 | 0.000 | |
Error | 0.713 | 6 | 0.119 | |||
Sum | 27.009 | 8 | ||||
ηql | Model | 0.176b | 2 | 0.088 | 1.435 | 0.309 |
E | 0.176 | 2 | 0.088 | 1.435 | 0.309 | |
Error | 0.368 | 6 | 0.061 | |||
Sum | 0.544 | 8 | ||||
a. R2=0.974(R2adj=0.965) b. R2=0.324(R2adj=0.098) |
(6) Influence of the soil patting plate gap on the soil removal effect
A picking roller gap of 0 mm, with better comprehensive soil removal rate, was used, and the other parameter values were the same as those in section (5). A single-factor test was conducted on the picking roller speed. Each factor level was repeated three times, and the mean value was taken. The results are shown in Figure 11.
Figure 11 shows that, with an increasing soil patting plate gap, the comprehensive soil removal rate and the soil removal pod drop rate both gradually decrease.
Analysis of variance at a significance level of α=0.05 was performed on the test results, as shown in Table 10. As shown in Table 10, the effect of the soil patting plate gap on the comprehensive soil removal rate and the soil removal pod drop rate is extremely significant. The analysis revealed that, as the soil patting plate gap gradually increased, the impact of the two soil patting plates on the peanut seedlings, soil, and pods gradually weakened, so the comprehensive soil removal rate and the soil removal pod drop rate gradually decreased, and the influence on the two soil removal performance indicators was extremely significant.
Source of variance | Sum of squares | df | Mean squares | F value | Sig. | |
ηzq | Model | 6.032a | 2 | 3.016 | 23.001 | 0.002 |
F | 6.032 | 2 | 3.016 | 23.001 | 0.002 | |
Error | 0.787 | 6 | 0.131 | |||
Sum | 6.819 | 8 | ||||
ηql | Model | 3.229b | 2 | 1.615 | 19.978 | 0.002 |
F | 3.229 | 2 | 1.615 | 19.978 | 0.002 | |
Error | 0.485 | 6 | 0.081 | |||
Sum | 3.714 | 8 | ||||
a. R2=0.879(R2adj=0.839) b. R2=0.187(R2adj=−0.184) |
(7) Influence of clamping conveyor chain speed on the soil removal effect
Considering the smoothness of the peanut seedlings passing through (because when the gap between the soil patting plates is too small, peanut plants with a large range of pods will hang to the soil patting plates, resulting in poor passage), a soil patting plate gap of 100 mm, with better performance for both the comprehensive soil removal rate and the soil removal pod drop rate, was used, and the other parameter values were the same as those in section (6). A single-factor test was conducted on the clamping conveyor chain speed. Each factor level was repeated three times, and the mean value was taken. The results are shown in Figure 12.
Figure 12 shows that, with increasing clamping conveyor chain speed, the comprehensive soil removal rate and the soil removal pod drop rate both gradually decrease, and the comprehensive soil removal rate decreases faster.
Analysis of variance at a significance level of α=0.05 was performed on the test results, as shown in Table 11. As shown in Table 11, the effect of the clamping conveyor chain speed on the comprehensive soil removal rate is extremely significant and is significant for the soil removal pod drop rate.
Source of variance | Sum of squares | df | Mean squares | F value | Sig. | |
ηzq | Model | 10.889a | 2 | 5.445 | 28.725 | 0.001 |
G | 10.889 | 2 | 5.445 | 28.725 | 0.001 | |
Error | 1.137 | 6 | 0.190 | |||
Sum | 12.027 | 8 | ||||
ηql | Model | 0.858b | 2 | 0.429 | 5.693 | 0.041 |
G | 858 | 2 | 0.429 | 5.693 | 0.041 | |
Error | 0.452 | 6 | 0.075 | |||
Sum | 1.310 | 8 | ||||
a. R2=0.905(R2adj=0.874) b. R2=0.655(R2adj=−0.540) |
The analysis revealed that, as the clamping conveyor chain speed gradually increased, the time required for the peanut plants to pass through the gap between the two soil patting plates decreased. When the soil patting plate frequency is constant, the number of times peanut plants are hit by the soil plate decreases. When the speed reaches a certain extent, peanut plants even pass through the gap without being hit by the soil patting plate, which cannot achieve the effect of soil removal. Therefore, the clamping conveyor chain speed has an extremely significant impact on the comprehensive soil removal rate. Similarly, as the clamping conveyor chain speed gradually decreases, the number of effective patting times of the soil patting plate on peanut plants increases, so the soil removal pod drop rate gradually increases. However, when pods have a strong stem connection force and when the hitting force of the soil plate is less than the stem connection force, within a limited range of hitting times, the stem will not be broken; thus, the impact on the rate of the decrease in the number of pods removed from the soil is significant.
From the above analysis, it can be seen that the trends and significance of various operational parameters on the soil removal effect performance indicators are different. Due to the limitations of the harvest season, this study only included a preliminary study on the impact of various operational factors on a half-feed peanut-cleaning harvester in hilly areas.
To improve the comprehensive soil removal effect, future research can focus on the comprehensive influence of various factors and their interactions on various performance indicators and further analyze the influence of various agronomic and operational parameters on various performance indicators. Moreover, real-time monitoring of various operational parameters can also be performed to improve the adaptability of peanut pickers to different soil types in different regions.
(1) A new half-feed peanut-cleaning picker suitable for the southern clay hilly area was designed, and a detailed introduction to the overall structure and working principle was provided. The key factors affecting the soil removal effect and their adjustment methods, such as the soil patting plate frequency, soil patting plate amplitude (i.e., crank length), soil patting form (opposite swing direction, swing direction), picking roller speed and gap, soil patting plate gap, and clamping conveyor chain speed, were analyzed and determined.
(2) Field experiments were conducted on soil removal performance indicators such as comprehensive soil removal rate and soil removal pod drop rate, and the regularity and significance of the influence of various factors on the two performance indicators were analyzed. The results indicate that all factors have an extremely significant impact on the comprehensive soil removal rate. The frequency, amplitude, form, and gap of soil patting have an extremely significant impact on the soil removal pod drop rate. The clamping conveyor chain speed has a significant impact, while the speed and gap of the picking roller have no effect on the soil removal pod drop rate. This study can provide a technical reference for parameter optimization research on peanut-cleaning picking machines in the clay hilly areas of southern China.
This study was financially supported by the Jiangsu Agricultural Science and Technology Innovation Fund (Grant No. CX(23)3028), National Natural Science Foundation of China (Grant No. 52105263), Key Laboratory of Modern Agricultural Intelligent Equipment in South China, Ministry of Agriculture and Rural Affairs, China (Grant No. HNZJ202201), Key Laboratory of Agricultural Equipment for Hilly and Mountainous Areas in Southeastern China (Co-construction by Ministry and Province), Ministry of Agriculture and Rural Affairs (Grant No. QSKF202304), and Key Laboratory of Intelligent Equipment and Robotics for Agriculture of Zhejiang Province (Grant No. 2022ZJZD2201).
[1] |
Wang S Y, Hu Z C, Chen Y Q, Wu H C, Wang Y W, Wu F, Gu F W. Integration of agricultural machinery and agronomy for mechanized peanut production using the vine for animal feed. Biosystems Engineering, 2022(219): 135–152. DOI: 10.1016/j.biosystemseng.2022.04.011
|
[2] |
Wang S Y, Hu Z C, Peng B L, Wang B, Wang Y W. Simulation and parameter optimization of pickup device for full-feed peanut combine harvester. Computers and Electronics in Agriculture, 2022; 192: 106602. DOI: 10.1016/j.compag.2021.106602
|
[3] |
Xu N, Shang S Q, Wang D W, He X N, Gao Z, Liu J Q, et al. Design and experimental study of a pin-type longitudinal axial flow peanut picking device. Journal of Agricultural Mechanization Research, 2020; 42(8): 197–201. DOI: 10.13427/j.cnki.njyi.2020.08.036
|
[4] |
Wang Q, Yu Z, Zhang Y, Li J, Peng B, Wang B, et al. Experimental study of a 4HLB-4 half-feed four-row peanut combine harvester. Agronomy, 2022; 12, 3094.
|
[5] |
Gao L X, Chen Z Y, Chen C, Butts C L. Development course of peanut harvest mechanization technology of the United States and enlightenment to China. Transactions of the CSAE, 2017; 33(12): 1–9. (in Chinese) DOI: 10.11975/j.issn.1002-6819.2017.12.001
|
[6] |
Yao L J, Hu Z C, Wang S Y, Cao M Z, Wang B, Yu Z Y. Research status and key technology analysis of peanut harvester. Jiangsu Agricultural Sciences, 2016; 44(12): 33–38. (in Chinese) DOI: 10.15889/j.issn.1002-1302.2016.12.008
|
[7] |
Wang ., Hu Z C, Peng B L, Zhang Y H, Gu F W, Shi L L, et al. Structure operation parameter optimization for elastic steel pole oscillating screen of semi-feeding four rows peanut combine harvester. Transactions of the CSAE, 2017; 33(21): 20–28. (in Chinese)
|
[8] |
Antiaobong E A, Bhattaraik R. Growth trends and sources of output growth for oil palm and groundnut production in Nigeria (1961-2007). Trends in Agricultural Economics, 2012; 5(3): 96–03. DOI: 10.3923/tae.2012.96.103
|
[9] |
Wang B B, Zhang X. Design and experiment of peanut harvester in South China. Modern Agricultural Equipment, 2020; 41(4): 33–38. (in Chinese)
|
[10] |
Chen Q M. 2022 China Agricultural Mechanization Yearbook. Beijing: China Agricultural Science and Technology Press, 2022. (in Chinese)
|
[11] |
Wang S Y, Hu Z C, Xu H B, Cao M Z, Yu Z Y, Peng B L. Design and test of pickup and conveyor device for full-feeding peanut pickup harvester. Transactions of the CSAE, 2019; 35(19): 20–28. (in Chinese) DOI: 10.11975/j.issn.1002-6819.2019.19.003
|
[12] |
Jaime C N. Current status and strategies for harvest mechanization of peanut in Mexico. SSRG International Journal of Agriculture & Environmental Science (SSRG-IJAES), 2015; 2(1): 7–15. https://www.researchgate.net/publication/275214348
|
[13] |
Liu Y C, He K, Wang Q, Geng D Y, Li Z P, Zhang S H. Design and experiment of 4HJZ-4A peanut collecting and picking machines. Agricultural Mechanization Research, 2019; 41(5); 121–126, 132. (in Chinese)
|
[14] |
Guo W H, Guo H, Yu X D, Wang M H, Xing S K, Peng B. Design and experiment of peanut digger based on two-stage harvesting process. Journal of Chinese Agricultural Mechanization, 2020; 41(7): 34–39. DOI: 10.13733/j.jcam.issn.2095-5553.2020.07.006
|
[15] |
Lv X R, Lv X L, Wang T Y, Zhang X Q, Zhang L H. Virtual simulation and experimental research of half-feed peanut picker. Journal of Northwest A&F University (Nat. Sci. Ed. ), 2020; 41 (4): 33–38. (in Chinese)
|
[16] |
Jiang Y J, Chen L D, Li G F, Wang Y F, Du F Y. The research progress on the peanut harvester digging device. Journal of Hebei Normal University of Science & Technology, 2021; 35(4): 59–63. Doi: 10. 3969/J. ISSN. 1672-7983. 2021. 04. 010 (in Chinese)
|
[17] |
Yu J D, Liu Y F, Wang D W. Design and experimental study of movable peanut picker. Agricultural Mechanization Research, 2021; 43(9): 59–65. DOI: 10.13427/j.cnki.njyi.2021.09.011
|
[18] |
Lv X L, Hu Z C, Zhang Y H, Wang B K. Study on properties of two-step type peanut stripping. Agricultural Mechanization Research, 2017(6): 183–187. DOI: 10.13300/j.cnki.hnlkxb.2015.03.037
|
[19] |
Wang T, Liu G G, Lou T T, Yao A P, Wu L H. Development and test of sweet potato harvester in hilly areas. Journal of Chinese Agricultural Mechanization, 2019; 40(12): 41–46, 71. DOI: 10.13733/j.jcam.issn.2095-5553.2019.12.08
|
[20] |
Zhang Z G, Wang H Y, Li Y B, Yang X, Ibrahim I, Zhang Z D. Design and experiment of multi-stage separation buffer potato harvester. Transactions of the CSAM, 2021; 52(2): 96–109. DOI: 10.6041/j.issn.1000-1298.2021.02.009
|
[21] |
Wang H Y, Zhang Z G, Ibrahim I, Xie K T, Wael E, Cao Q Z. Design and experiment of small-sized potato harvester suitable for hilly and mountainous areas. Acta Agriculturae Zhejiangensis, 2021; 33(4): 724–738.
|
[22] |
Xin S L, Zhao W Y, Shi L R, Dai F, Feng B, Yan Z B, et al. Design and experiments of the clamping and conveying device for the vertical roller type corn harvesting header. Transactions of the CSAE, 2023; 39(9): 34–43. DOI: 10.11975/j.issn.1002-6819.202211036
|
[23] |
Zhang J, Wang J, Du DD, Long S F, Wang Y W, You X R. Design and experiment of crawler self-propelled single-row harvester for Chinese cabbage. Transactions of the CSAM, 2022; 53(12): 134–146. DOI: 10.6041/j.issn.1000-1298.2022.12.013
|
[24] |
Feng Y L, Yin X C, Jin H R, Tong W Y, Ning X F. Design and experiment of a Chinese chive harvester. Int J Agric & Biol Eng, 2023; 16(2): 125–131. DOI: 10.25165/j.ijabe.20231602.7067
|
[25] |
Chen Z Y. Experimental study on axial-flow peanut picking device with benting-tooth screw roller. Shenyang: Shenyang Agricultural University, 2017.
|
[26] |
GB/T5262-2008, General regulations for the determination of test conditions for agricultural machinery.
|
[27] |
NY/T 502-2016, Operation quality of peanut harvesters.
|
[28] |
NY/T 2204-2012, Technical specification for quality evaluation of peanut harvesters.
|
Items | Value |
Picker size (length × width × height)/mm | 2600×950×1080 |
Distance adjustment range between soil removal device and clamping conveyor device/mm | 30-100 |
Distance adjustment range between soil removal device and picking device/mm | 50-200 |
Total mass of the picker/kg | 250 |
Matched power/kW | 3.3 |
Power-source form | Single cylinder gasoline engine |
Rated speed of power source/r·min–1 | 1800 |
Level | Factors | ||||||
A: Soil patting plate frequency/ Hz |
B: Soil patting plate amplitude (crank length)/ mm |
C: Soil patting form |
D: Picking roller speed/ r·min–1 |
E: Picking roller gap/ mm |
F: Soil patting plate gap/mm |
G: Clamping conveyor chain speed/ m·s–1 |
|
1 | 2.0 | 25 | 1 (Same direction swing) | 275 | 20 | 80 | 0.4 |
2 | 4.0 | 35 | –1 (Opposite direction swing) | 375 | 0 | 100 | 0.6 |
3 | 6.0 | 45 | / | 475 | -20 | 120 | 0.8 |
Soil patting plate frequencyA |
Comprehensive soil removal rate ηzq/% |
Soil removal pods drop rate ηql/% |
2.0 | 92.18 | 2.28 |
2.0 | 93.20 | 2.69 |
2.0 | 91.79 | 2.72 |
4.0 | 96.75 | 4.77 |
4.0 | 96.48 | 3.94 |
4.0 | 97.24 | 4.39 |
6.0 | 97.83 | 4.43 |
6.0 | 97.69 | 4.45 |
6.0 | 98.11 | 4.95 |
Source of variance | Sum of squares | df | Mean squares | F value | Sig. | |
ηzq | Model | 50.867a | 2 | 25.434 | 105.350 | 0.000 |
A | 50.867 | 2 | 25.434 | 105.350 | 0.000 | |
Error | 1.449 | 6 | 0.241 | |||
Sum | 52.316 | 8 | ||||
ηql | Model | 7.500b | 2 | 3.750 | 35.171 | 0.000 |
A | 7.500 | 2 | 3.750 | 35.171 | 0.000 | |
Error | 0.640 | 6 | 0.107 | |||
Sum | 10.102 | 8 | ||||
a. 0.972(R2adj=0.963) b. R2=0.921(R2adj=0.895) |
Source of variance | Sum of squares | df | Mean squares | F value | Sig. | |
ηzq | Model | 68.953a | 2 | 34.476 | 222.428 | 0.000 |
B | 68.953 | 2 | 34.476 | 222.428 | 0.000 | |
Error | 0.930 | 6 | 0.155 | |||
Sum | 69.883 | 8 | ||||
ηql | Model | 13.375b | 2 | 6.688 | 102.239 | 0.000 |
B | 13.375 | 2 | 6.688 | 102.239 | 0.000 | |
Error | 0.392 | 6 | 0.065 | |||
Sum | 13.768 | 8 | ||||
a. R2=0.987(R2adj=0.982) b. R2=0.971(R2adj=0.962) |
Soil patting form C | Comprehensive soil removal rate ηzq/% | Mean of comprehensive soil removal rate/% | Soil removal pods drop rate ηql/% | Mean of soil removal pods drop rate/% |
1 | 92.32 | 92.25 | 2.38 | 2.33 |
1 | 91.98 | 2.21 | ||
1 | 92.44 | 2.41 | ||
–1 | 96.75 | 96.82 | 4.77 | 4.37 |
–1 | 96.48 | 3.94 | ||
–1 | 97.24 | 4.39 |
Source of variance | Sum of squares | df | Mean squares | F value | Sig. | |
ηzq | Model | 31.419a | 2 | 31.419 | 305.978 | 0.000 |
C | 31.419 | 2 | 31.419 | 305.978 | 0.000 | |
Error | 0.411 | 6 | 0.103 | |||
Sum | 31.830 | 8 | ||||
ηql | Model | 6.202b | 2 | 6.202 | 67.312 | 0.001 |
C | 6.202 | 2 | 6.202 | 67.312 | 0.001 | |
Error | 0.369 | 6 | 0.092 | |||
Sum | 6.570 | 8 | ||||
a. R2=0.987(R2adj=0.984) b. R2=0.944(R2adj=0.930) |
Source of variance | Sum of squares | df | Mean squares | F value | Sig. | |
ηzq | Model | 147.344a | 2 | 73.672 | 288.232 | 0.000 |
D | 147.344 | 2 | 73.672 | 288.232 | 0.000 | |
Error | 1.534 | 6 | 0.256 | |||
Sum | 148.878 | 8 | ||||
ηql | Model | 0.311b | 2 | 0.155 | 1.540 | 0.288 |
D | 0.311 | 2 | 0.155 | 1.540 | 0.288 | |
Error | 0.605 | 6 | 0.101 | |||
Sum | 0.915 | 8 | ||||
a. R2=0.990(R2adj=0.986) b. R2=0.339(AR2adj=0.119) |
Source of variance | Sum of squares | df | Mean squares | F value | Sig. | |
ηzq | Model | 26.296a | 2 | 13.148 | 110.654 | 0.000 |
E | 26.296 | 2 | 13.148 | 110.654 | 0.000 | |
Error | 0.713 | 6 | 0.119 | |||
Sum | 27.009 | 8 | ||||
ηql | Model | 0.176b | 2 | 0.088 | 1.435 | 0.309 |
E | 0.176 | 2 | 0.088 | 1.435 | 0.309 | |
Error | 0.368 | 6 | 0.061 | |||
Sum | 0.544 | 8 | ||||
a. R2=0.974(R2adj=0.965) b. R2=0.324(R2adj=0.098) |
Source of variance | Sum of squares | df | Mean squares | F value | Sig. | |
ηzq | Model | 6.032a | 2 | 3.016 | 23.001 | 0.002 |
F | 6.032 | 2 | 3.016 | 23.001 | 0.002 | |
Error | 0.787 | 6 | 0.131 | |||
Sum | 6.819 | 8 | ||||
ηql | Model | 3.229b | 2 | 1.615 | 19.978 | 0.002 |
F | 3.229 | 2 | 1.615 | 19.978 | 0.002 | |
Error | 0.485 | 6 | 0.081 | |||
Sum | 3.714 | 8 | ||||
a. R2=0.879(R2adj=0.839) b. R2=0.187(R2adj=−0.184) |
Source of variance | Sum of squares | df | Mean squares | F value | Sig. | |
ηzq | Model | 10.889a | 2 | 5.445 | 28.725 | 0.001 |
G | 10.889 | 2 | 5.445 | 28.725 | 0.001 | |
Error | 1.137 | 6 | 0.190 | |||
Sum | 12.027 | 8 | ||||
ηql | Model | 0.858b | 2 | 0.429 | 5.693 | 0.041 |
G | 858 | 2 | 0.429 | 5.693 | 0.041 | |
Error | 0.452 | 6 | 0.075 | |||
Sum | 1.310 | 8 | ||||
a. R2=0.905(R2adj=0.874) b. R2=0.655(R2adj=−0.540) |